Characteristics of the CompuLathe:
- Elegant Visual Reference System
- No G-code or M-code required for programming
- True GUI (User Graphic Interface)
- Multiple programming methods built-in
- Soft and Hard Emergency Stop Buttons
- Sensor detects the rotation speed of the spindle motor and is able to respond appropriately to abrupt changes in rotational speeds (optional)
- Instant image capturing feature (optional)
- Digital camera monitoring and remote control machine operation via network or internet access (optional)
- Optional accessories include touch sensor and indicator interfaces
Inside of CompuLathe
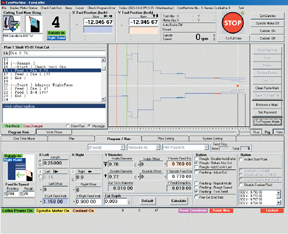
Features of the CompuLathe Navigator
- Sound Notification and Warning
- AutoBrake to suspend movement
- Programmable computer-controlled coolant dispensing system
- Three different ways of tracking the target position
- User definable Tools Library with full animation
- Special technique on cut-off function of work piece
- Automatically updates the position of the slave of the cutting tools when any of the defined cutting tools is changed
- Changes motor speed on the fly during job processing
- Synchronous toolpath display
- Easy to define coordinates for cutting tool
- Real time display positioning includes XY-tool, target positions and absolute counters, the speed of the motor and the stage of the job being machined
- Variable view window with zoom in and out capabilities
Three methods for programming the lathe jobs
Off-line programming: Pre-program lathe jobs without the machine being manned.
Single Move: Allows a user to manually define a movement of the cutting tool on the X or Y axis step by step.
Program/Run: Nine command modes to program the lathe job. There are many features included:
One click button to program complex procedures
On-line access Visual Reference System
Instant simulation tool path of the lathe job; enables user to compare different methods of tool path processing
Labeling reference marks on important intersection of the work piece as a guideline to do position changes or offsetting
Program complex lathe jobs and execute them with the click of a button
Fine Cut End Side: Smooth the last feed process for eliminating any outstanding indentions left by the previous horizontal feeds.
Roughing - Add Reverse Cut: Roughly cut the work piece. Metal shavings will be smaller and less tangled, making the work area easier to maintain.
Roughing - Add cut at last: Add an extra feed process at the second last part of the feed order to make sure the final feed has less resistance, insuring a smooth finishing cut.
Finishing- Adjust Cut Vector: Adjust the path of the cutting tool to compensate for melted mass or friction wear on the cutting tool.
Finishing - Twin Feed: Insert second round cut to feed in between the gap of the first round cut, giving the surface a perfect finish.
Incline Starting Point: Use a cutting tool that is oriented to cut from the left side.
Threading Insert-Constant Cut Depth: Set all feed orders into the work piece at a constant measurement.
Capture your experience as a guideline to standardize the machining procedure
The Visual Reference System is designed for recording a procedure of a lathe job by capturing an image which is combined with the programming job for the operator to follow step by step. There are many advantages to this system:
- Prevention of man-made errors
- Ability to help operators of different skill levels to machine precise work
- Standardization of lathe job processes
- Saving time on set-up, adjustment and maintenance during operation
The images may include set-up guidelines, position of the work piece and tools, tooling preparation or adjustment and maintenance during the operation. Recording these events guarantees every job is of the same quality.
There are two ways to activate the Visual Reference System. Pictures can be imported to the program/run mode. Alternatively, the Visual Reference System can capture an image using a digital camera that is directly linked to the CompuLathe Navigator (optional accessories).
Remote control Machine Operation
A digital camera is provided to monitor the work process. Images are sent to a server via a network for remote control purposes. The server is dialogue capable, which can alert an operator by a computer synthesized voice during important, pre-programmed occasions.
Accessories
Touch Sensor
The Touch Sensor is able to detect a cutting tool on contact. The information gathered is sent to the computer and calculated. The positioning of the coordinates of the cutting tool and work piece can be found through a series of operations using the touch sensor.
Indicator interface
The indicator is a third party sensor that can be linked to the CompuLathe system. It can be used to detect the position of the work piece along the x-axis.